Awe-Inspiring Examples Of Info About Who Is Responsible For Bill Of Materials
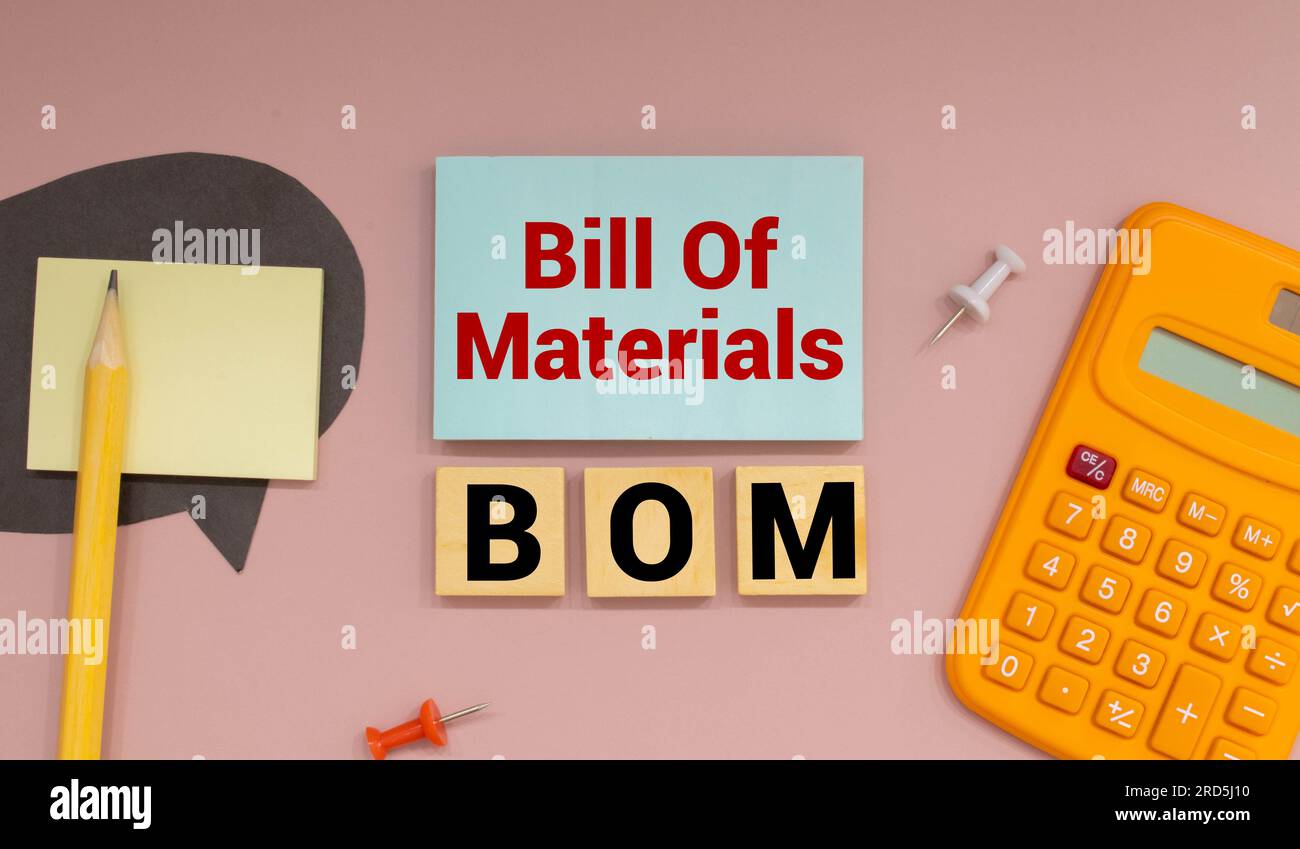
Unraveling the Mystery
1. Decoding the BOM Responsibility Puzzle
Ever wondered who's actually in charge of that crucial document, the Bill of Materials (BOM)? It's not always a single person waving a magic BOM wand! Think of it more like a team effort, a relay race where different departments contribute their piece of the puzzle. Getting it right is super important because the BOM basically dictates what goes into your product, from the tiniest screw to the biggest circuit board. Messing it up can lead to production delays, cost overruns, and products that...well, just don't work!
So, let's dive into the cast of characters who typically play a role. We're talking engineers, procurement specialists, manufacturing teams, and sometimes even sales and marketing. Each brings a unique perspective and contributes to the BOM's accuracy and completeness. It's less about finding one "responsible" person and more about understanding how each role fits into the overall BOM process. It's like a symphony, where each instrument plays its part to create beautiful (and functional!) music.
The complexity can also depend on the size of the company. In smaller businesses, one person might wear many hats, juggling engineering, purchasing, and even some manufacturing responsibilities. In larger organizations, the roles are often more specialized, with dedicated BOM managers or teams overseeing the entire process. No matter the size, clear communication and collaboration are absolutely key.
Ultimately, while specific roles vary by company, the responsibility for a well-maintained and accurate BOM rests collectively across multiple departments. The trick is fostering a culture of ownership and accountability, where everyone understands the importance of their contribution to the final product.
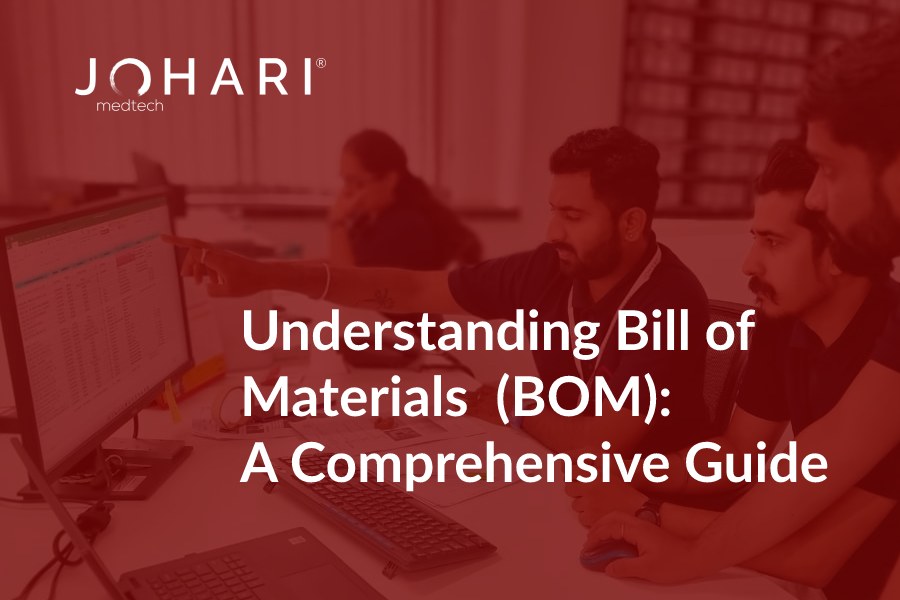
The Core Crew
2. Meet the Usual Suspects
Okay, so who are these folks we're talking about? Let's break down the main players and their typical roles in the BOM drama.
First up, we've got the Engineers. These are the designers, the creative minds who dream up the product in the first place. They specify the components needed, their technical specifications, and how they all fit together. They're the architects of the BOM, laying the foundation for everything that follows. Think of them as the authors of the BOM's first draft, constantly revising and refining as the design evolves.
Next, enter the Procurement Team (or Purchasing). Once the engineers have specified the parts, it's the procurement team's job to find suppliers, negotiate prices, and ensure timely delivery. They're the budget hawks, always looking for ways to optimize costs without compromising quality. They ensure that the right parts, at the right price, get to the right place at the right time. They're the logistical ninjas of the BOM world.
Then comes the Manufacturing Team. These are the people who actually build the product! They rely on the BOM to understand exactly what components are needed and how to assemble them. They're the hands-on experts, providing feedback on manufacturability and identifying any potential issues with the BOM. They're the ultimate test of the BOM's accuracy and completeness.
And don't forget the Quality Assurance (QA) Team. They ensure that the components and the finished product meet the required quality standards. They rely on the BOM to verify that the correct parts are used and that the assembly process is followed correctly. They're the gatekeepers, ensuring that only high-quality products make it to market.

Bill Of Materials On Blue Stock Illustration. Illustration
BOM Management
3. It's a Process, Not Just a List
Think a BOM is just a simple spreadsheet? Think again! Effective BOM management involves a whole lot more than just listing parts. It's about establishing clear processes, utilizing the right tools, and fostering collaboration across departments.
One crucial aspect is version control. As products evolve and designs change, the BOM needs to be updated accordingly. Proper version control ensures that everyone is working with the latest and greatest version, preventing costly mistakes. It's like having a single source of truth, eliminating confusion and ensuring consistency.
Another important element is change management. When a component needs to be changed, a formal process should be followed to ensure that all affected departments are notified and that the change is properly documented. This prevents unauthorized changes and ensures that everyone is on the same page. It's about controlling the chaos and maintaining order in the BOM universe.
Modern BOM management often involves using specialized software, such as Product Lifecycle Management (PLM) systems or Enterprise Resource Planning (ERP) systems. These systems provide a centralized repository for all BOM data, making it easier to manage and track changes. They also facilitate collaboration and communication between departments. Think of them as the command center for your BOM operations.
Ultimately, effective BOM management is about creating a culture of accuracy and accountability. It's about empowering everyone involved to take ownership of the BOM and to contribute to its success. It's a team effort, where everyone plays a crucial role in ensuring that the product is built correctly and efficiently.
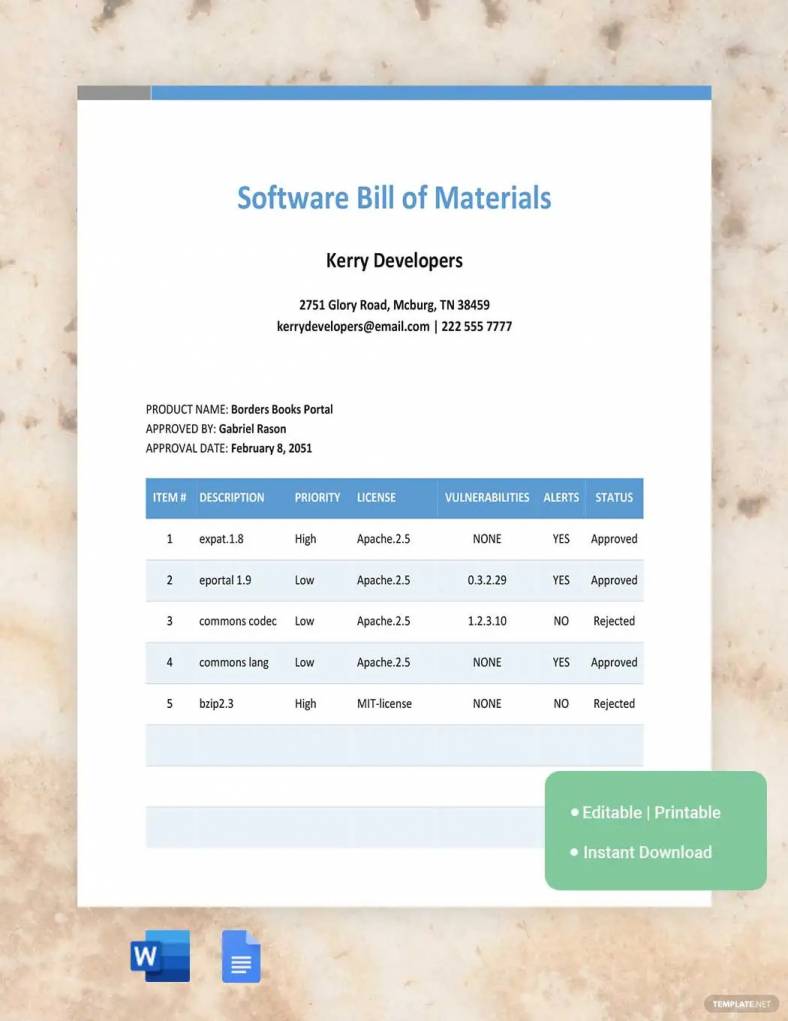
Bill Of Material What Is A Material? Definition, Types, Uses
The Consequences of a Botched BOM
4. Why Accuracy Matters (A Lot!)
So, what happens when the BOM goes wrong? The consequences can range from minor inconveniences to major disasters. Let's explore some of the potential pitfalls of a poorly managed BOM.
One common consequence is production delays. If the BOM contains incorrect information, such as the wrong part numbers or quantities, it can lead to shortages or the use of incorrect components. This can halt production and delay product launches, costing the company time and money. Imagine the frustration of your manufacturing team when they can't find the right part!
Increased costs are another potential consequence. Incorrect BOMs can lead to over-ordering of some parts and under-ordering of others, resulting in wasted inventory and the need for rush orders. This can significantly increase the cost of goods sold and erode profit margins. It's like throwing money down the drain!
Quality problems can also arise from inaccurate BOMs. If the wrong components are used, the finished product may not meet the required quality standards. This can lead to customer dissatisfaction, warranty claims, and even product recalls. Think of the damage to your brand reputation!
In extreme cases, a botched BOM can even lead to safety hazards. If critical components are missing or incorrect, the product may not function safely, putting users at risk. This is especially true for products in industries such as aerospace, medical devices, and automotive. The stakes are incredibly high!
Bill Of Material (BOM) PDF
FAQ
5. Everything You Wanted to Know (But Were Afraid to Ask)
Let's tackle some frequently asked questions about BOM responsibility. Consider this your BOM crash course!
6. Q
A: While several departments contribute, the responsibility is shared. However, engineering often takes the lead in the initial creation and maintenance, while a designated BOM manager (if the company has one) often oversees the entire process. The ultimate accuracy rests on the collective efforts of all involved.
7. Q
A: Investigate immediately! Identify the source of the error, correct the BOM, and implement preventative measures to avoid recurrence. Communication is key to resolving the issue quickly and efficiently.
8. Q
A: The BOM should be reviewed and updated whenever there are design changes, component substitutions, or process improvements. Regular audits are also a good idea to ensure accuracy and identify potential issues proactively. It's a living document that needs constant attention.
9. Q
A: Yes. The EBOM, or Engineering Bill of Materials, is design-focused, capturing the product's components and structure from an engineering perspective. It's created during the design phase. The MBOM, or Manufacturing Bill of Materials, is production-focused, detailing how a product is assembled, including packaging materials and any steps that may not be reflected in the EBOM.