Exemplary Tips About Can We Use BLDC Motor Without Controller
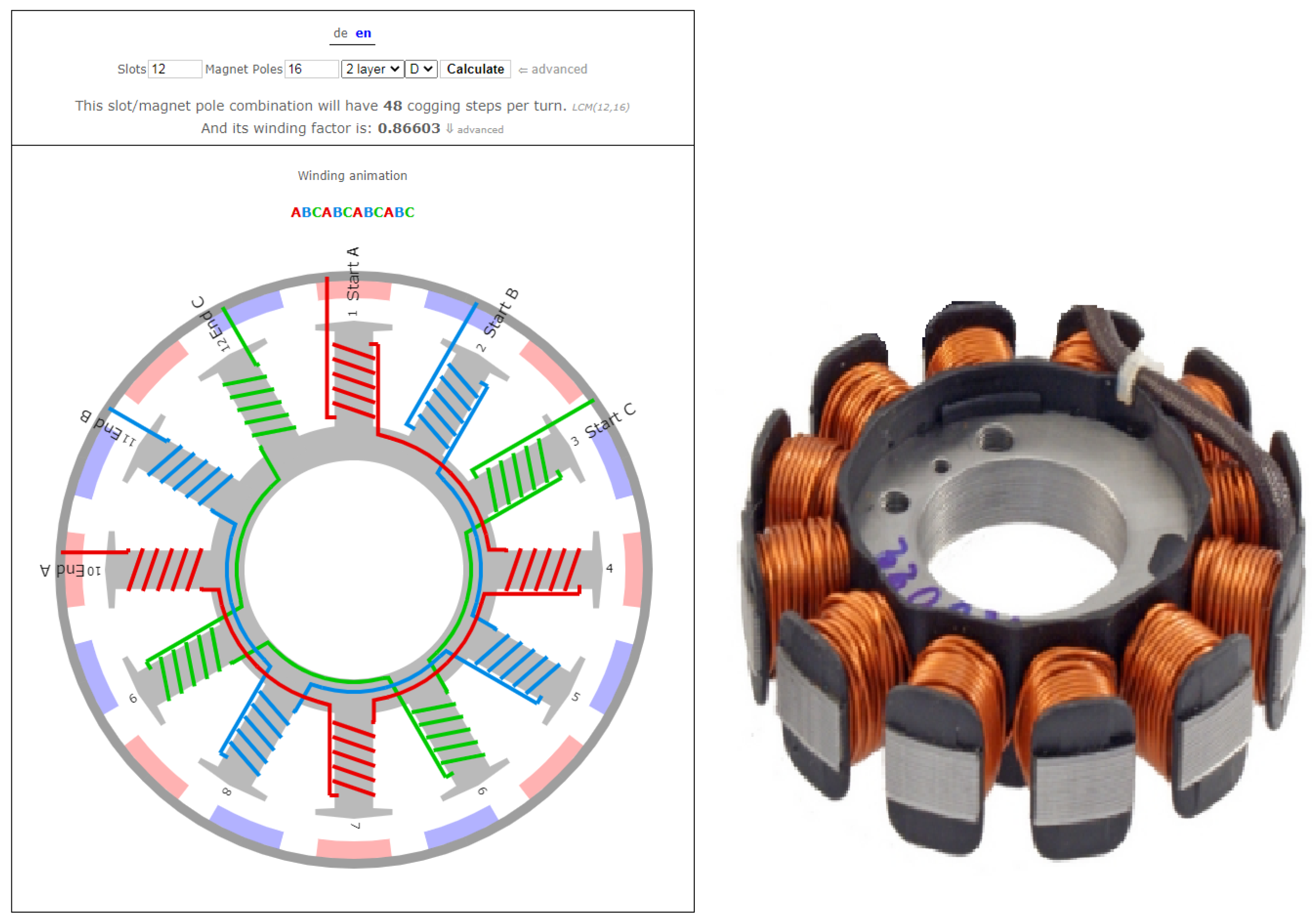
BLDC Motors — To Control or Not To Control? That Is The Question!
1. Understanding the Basics of BLDC Motors
So, you're wondering if you can just hook up a BLDC (Brushless DC) motor and watch it spin like a whirling dervish without any electronic shenanigans. Well, hold your horses! BLDC motors are a bit more sophisticated than your average DC motor. They don't have brushes (hence the "brushless" part), which is great for longevity and reducing maintenance. But this also means they need some external help to get their groove on.
Unlike brushed DC motors where the mechanical commutator handles the switching of current, BLDC motors rely on electronic commutation. This is where the motor controller comes into play. Think of the controller as the motor's brain, telling it which coils to energize and when to do it. Without this brain, the motor is essentially a bunch of wires and magnets just sitting there, looking pretty but not doing much else.
Imagine trying to drive a car without a steering wheel. You might get it to move, but controlling where it goes? Good luck with that! A BLDC motor without a controller is kind of the same situation. You need that controller to dictate the speed, direction, and overall performance of the motor. Otherwise, you're in for a bumpy, unpredictable ride — metaphorically speaking, of course.
Essentially, the controller uses feedback (usually from Hall effect sensors or encoders) to determine the rotor's position. It then uses this information to sequentially energize the stator windings, creating a rotating magnetic field that pulls the rotor along. This synchronized dance between the controller and the motor is what produces smooth, efficient motion.
2. The Role of the BLDC Motor Controller
Let's delve a bit deeper into why the controller is the unsung hero of the BLDC motor world. The controller isn't just about turning the motor on and off. It's about precise control. It regulates the voltage and current supplied to the motor windings, allowing you to adjust the speed and torque as needed.
Think of it like this: you have a blender. Without the speed settings, you're stuck with either full power or nothing. A BLDC controller is like the blender's speed settings, giving you the ability to finely tune the motor's output to suit your specific application. Need a gentle stir? No problem. Need to pulverize ice? Crank it up! The controller gives you that flexibility.
Furthermore, the controller provides crucial protection for the motor. It can prevent overcurrent, overvoltage, and overheating, all of which can damage the motor if left unchecked. It's like having a bodyguard for your motor, constantly watching out for potential threats and intervening when necessary. This helps extend the motor's lifespan and ensures reliable operation.
Some advanced BLDC motor controllers even offer features like regenerative braking, which allows you to recover energy when the motor is slowing down. This energy can then be used to recharge a battery or power other components in your system, increasing efficiency and reducing energy consumption. It's like getting free energy just for slowing down — pretty neat, huh?
3. Can We Technically Use a BLDC Motor Without a Controller?
Okay, let's get down to brass tacks. Can you technically make a BLDC motor spin without a dedicated controller? The answer is a qualified yes, but with a HUGE asterisk attached. You could manually switch the phases to energize the windings, essentially mimicking what the controller does. But this is wildly impractical and inefficient. It would be like trying to write a novel by hand using only hieroglyphics — possible, but definitely not recommended!
The reason this is so difficult is that you need to precisely time the switching of the phases based on the rotor's position. This requires constant monitoring and adjustment, which is virtually impossible to do accurately by hand. The motor would likely run erratically, produce little torque, and potentially overheat. It's a recipe for disaster, to be honest.
Furthermore, without a controller, you lose all the benefits of precise control and protection. You can't adjust the speed or torque, and you run the risk of damaging the motor due to overcurrent or overheating. It's like driving that car without a steering wheel AND without brakes. Not a fun experience.
So, while it's theoretically possible to use a BLDC motor without a controller, it's highly impractical and not recommended for any real-world application. You're much better off investing in a decent controller that will allow you to get the most out of your motor and protect it from damage.
4. Practical Applications and the Importance of the Controller
Think about the applications where BLDC motors really shine: electric vehicles, drones, robotics, and high-precision machinery. In all of these cases, precise control is absolutely critical. An electric vehicle needs smooth acceleration and deceleration, a drone needs stable flight, a robot needs accurate movements, and precision machinery needs consistent performance.
Imagine a drone trying to maintain its altitude without a BLDC motor controller. It would be all over the place, constantly overshooting and undershooting its target. Or picture an electric vehicle with jerky, unpredictable acceleration. Not exactly a smooth and enjoyable ride, is it? The controller is what makes these applications possible by providing the necessary level of control and precision.
Moreover, the controller allows for advanced control algorithms like field-oriented control (FOC), which further enhances the motor's efficiency and performance. FOC allows the controller to independently control the torque and flux of the motor, resulting in smoother, more responsive operation. This is particularly important in applications where high dynamic performance is required, such as robotics and servo drives.
In conclusion, while the motor itself is a marvel of engineering, it's the controller that unlocks its full potential. It provides the brains and the brawn necessary to deliver precise, efficient, and reliable performance. So, if you're planning on using a BLDC motor, don't skimp on the controller. It's an investment that will pay off in the long run.
5. Choosing the Right Controller
So you're convinced a controller is a must-have. Great! But with so many options out there, how do you choose the right one? Well, there are a few key factors to consider. First and foremost, you need to match the controller's voltage and current ratings to the motor's specifications. Using an under-rated controller can lead to it overheating and failing, while an over-rated controller might be overkill and unnecessarily expensive.
Next, consider the control method. Some controllers use simple trapezoidal control, while others use more advanced sinusoidal or field-oriented control (FOC). FOC generally provides better performance in terms of smoothness, efficiency, and torque control, but it also requires more sophisticated hardware and software.
Also, think about the features you need. Do you need regenerative braking? Do you need the ability to communicate with other devices via CAN bus or other communication protocols? Do you need built-in protection features like overcurrent and overvoltage protection? Make a list of your requirements and look for a controller that meets them.
Finally, don't forget to consider the price. Controllers can range from relatively inexpensive to quite pricey, depending on their features and performance. Set a budget and try to find the best controller you can afford within that budget. Remember, it's better to invest in a good quality controller that will last and provide reliable performance than to skimp on price and end up with a headache down the road.

Simple How To Run BLDC Motor Without Driver YouTube
Frequently Asked Questions (FAQs)
6. Q
A: Yes, you generally can. A sensorless controller estimates the rotor position without relying on physical sensors. If your motor has sensors, you simply wouldn't connect them. However, a sensored controller cannot be used with a sensorless motor, as it requires sensor input to function.
7. Q
A: Connecting the phases incorrectly will likely cause the motor to spin in the opposite direction or not spin at all. It might also cause unusual vibrations or noises. Most controllers allow you to reverse the direction of rotation in the software, so it's usually an easy fix. Just double-check the wiring diagram before powering on the motor.
8. Q
A: Not all of them, but many are. Programmable controllers allow you to customize various parameters, such as acceleration rates, braking force, and current limits. This gives you greater flexibility in tuning the motor's performance to your specific application. If you need a high degree of control and customization, look for a programmable controller.
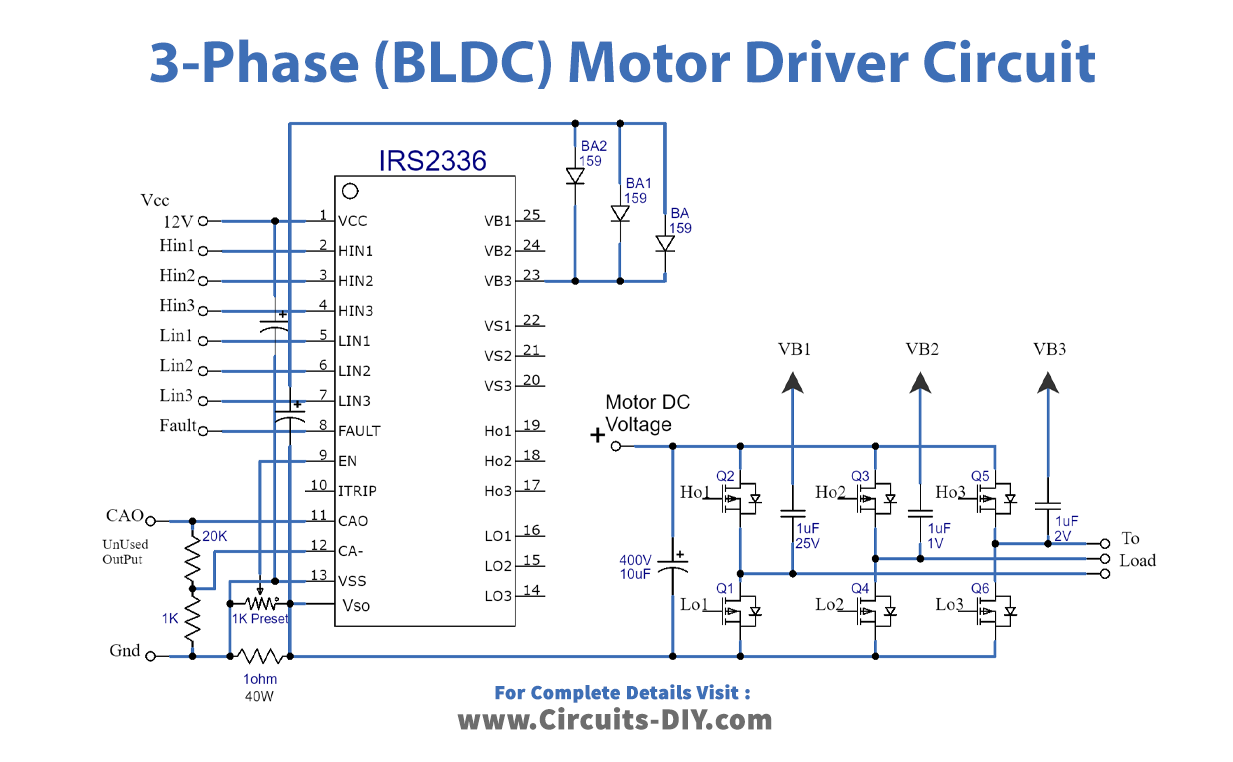
How To Build A 3 Phase Brushless BLDC Motor Driver Circuit
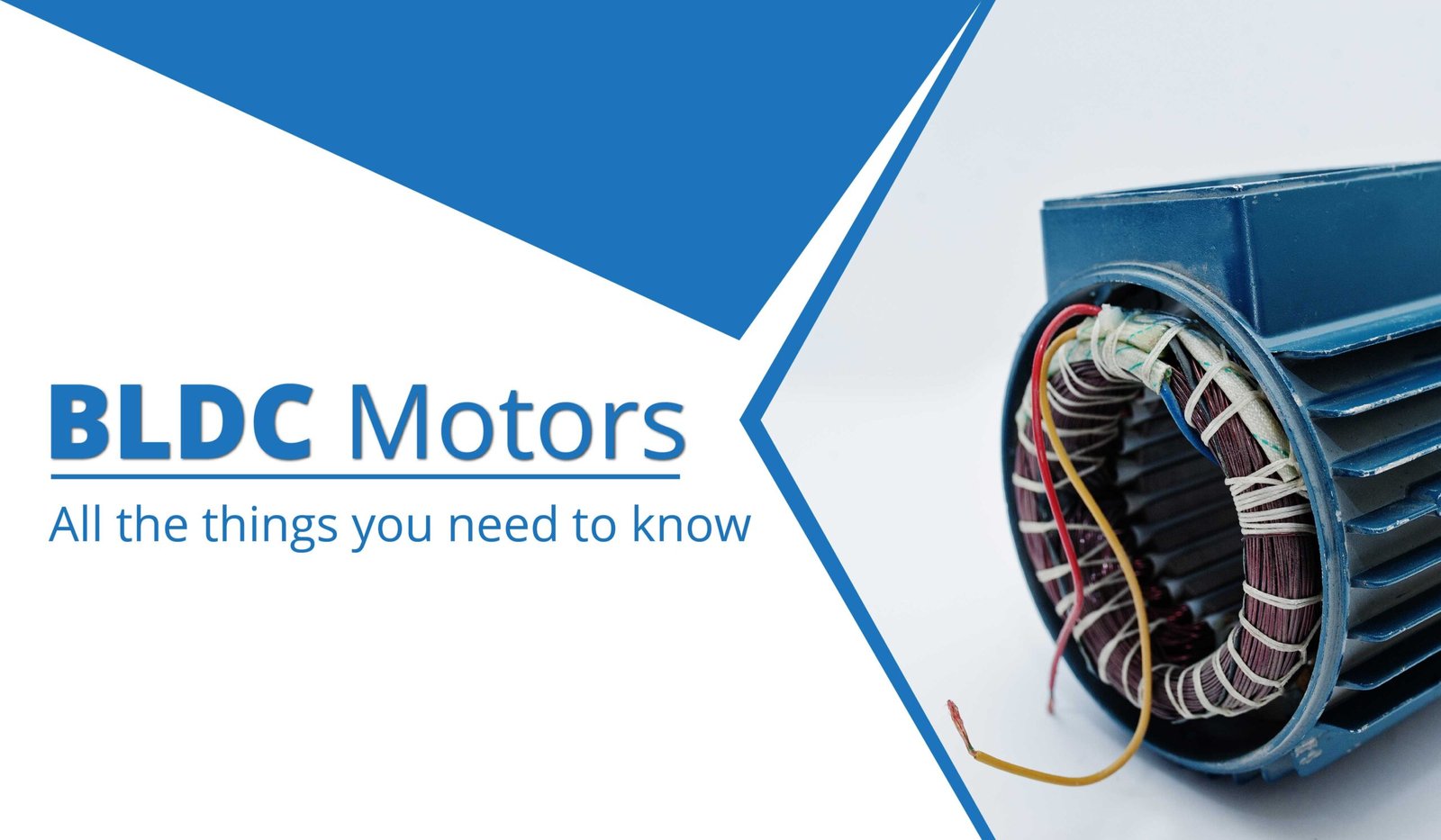
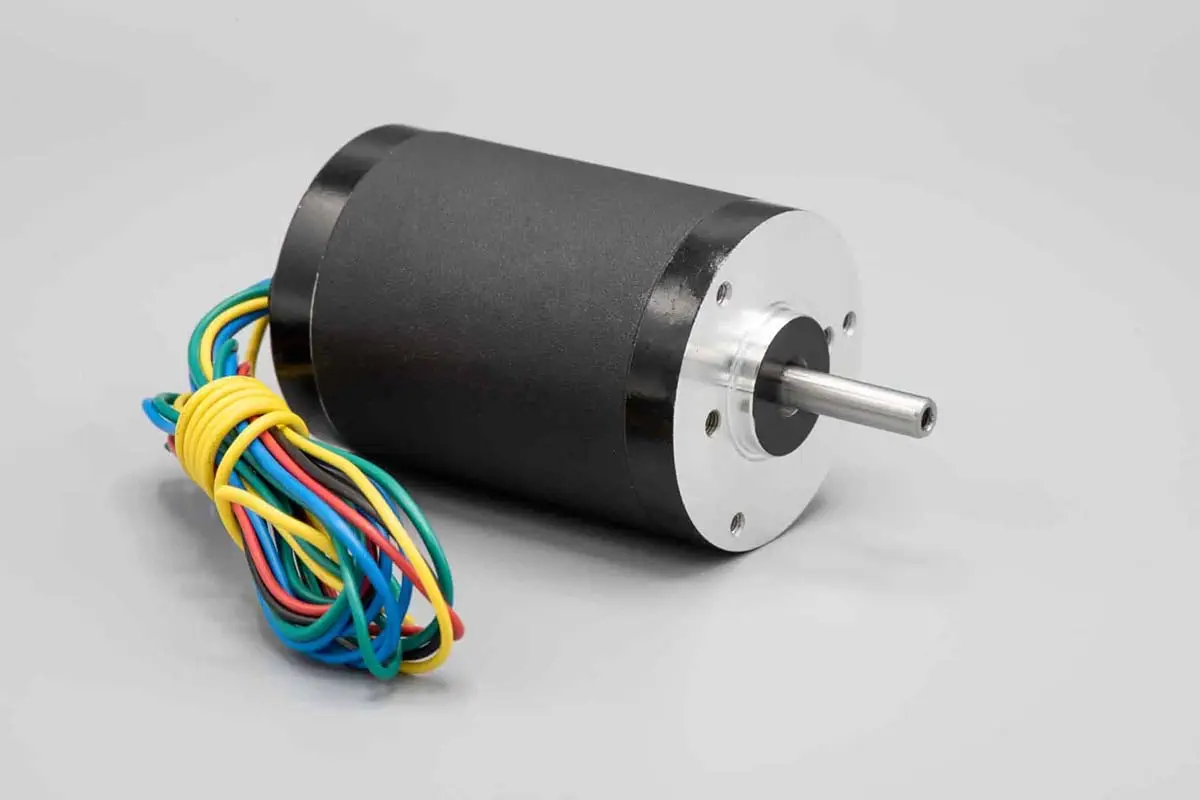
Brushless (BLDC) Motors & Gear ISL Products
